Wet Compression Test
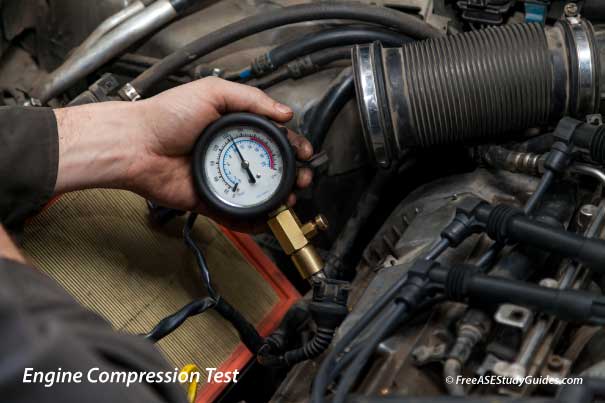
Cylinder compression tests identify combustion engine cylinders with poor compression. If a cylinder has low compression, perform a wet compression test to indicate whether a bad valve, head gasket, or worn piston rings are causing the problem.
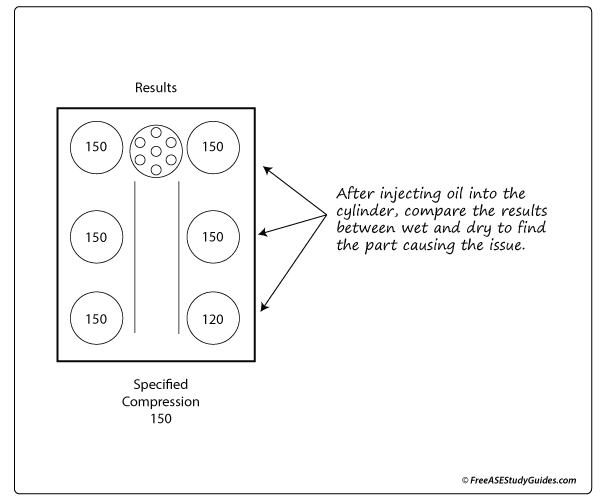
To perform this test, inject about a teaspoon of oil into the weak cylinder through the spark plug hole and screw the compression gauge back in.
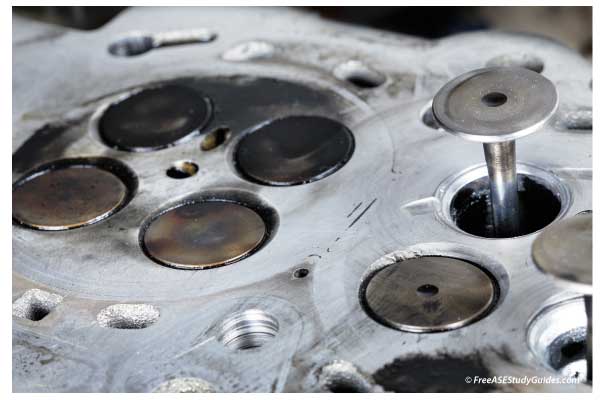
Introducing oil into a cylinder with worn piston rings increases the cylinder's compression. The oil fills the gap between the worn rings and the cylinder wall. If there is no increase in compression after running the test, an intake or exhaust valve is faulty.
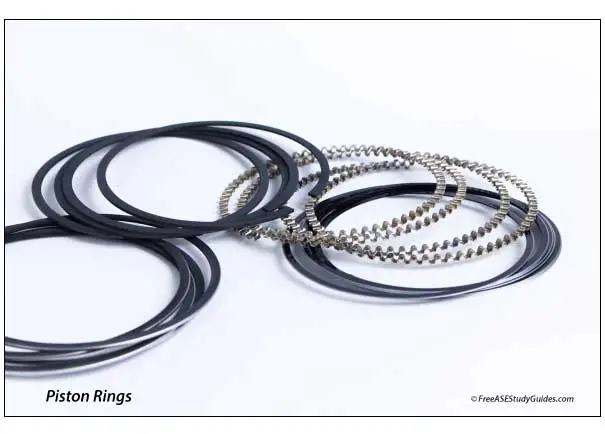
A compression test can be used to compare the compression of one cylinder to the others. An engine's cylinders need a good seal between the piston rings and the cylinder walls and between the valves and their respective seats.
Wet Compression Test Diagnosis
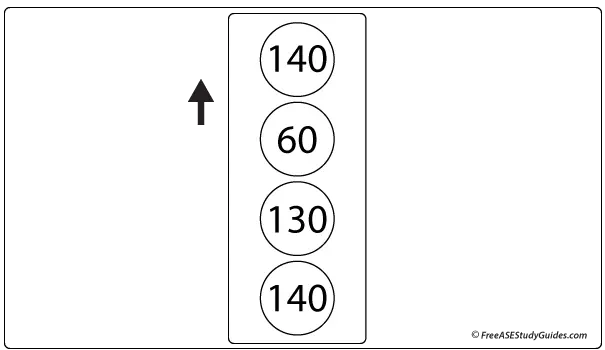
The results of a compression test can be quite telling. The results shown below indicate the particular area that needs attention.
Worn piston rings/cylinder walls: After running the first test, squirt a teaspoon of oil into the cylinder and rotate the crankshaft six turns. If the compression increases, the piston rings are at fault.
Burned valves: If the results remain the same, one or more of the cylinder's valves are bad or not sitting correctly. Low compression in only one cylinder typically indicates a bad valve. Exhaust valves are more likely to burn due to hot gases passing through. Intake valves have the added advantage of fuel flow, keeping them cooler.
Valve timing: When all of the cylinders are low and inserting oil into the cylinder does not increase compression, the camshaft timing is likely off. The timing belt can slip on the sprockets resulting in staggered and low compression results.
A hole in the piston: A hole in a piston will result in no compression in that cylinder. Remove the oil cap or PCV valve from its grommet. Blowby caused by this hole can be seen seeping through these openings.
Carbon buildup: Carbon buildup on the top of a piston increases compression readings. View the buildup with a probe inserted into the cylinder.
A faulty head gasket: A faulty or blown head gasket will leak compression between two adjacent cylinders. When the other cylinders are within specifications, and two adjacent cylinders on the same bank are low, suspect a faulty head gasket.